How long do water heaters really last?
MRT Home Inspections Article - 11/2023 | by Tyler Cole
I have noticed some comments from clients and realtors that water heaters only last about 10 years and that figure seemed odd to me given the fact that many inspected homes have water heaters older than that figure. I did some research on the internet and found numerous websites stating the life expectancy of the common tank style water heater as 8 to 12 years. I realized that I likely have the answer contained in the archive of my home inspection reports. After an exhaustive review of thousands of inspections, I arrived at the actual age range of 12 to 16 years. Learn more by following this link to the full article: Water Heater Age - The Real Data.
The Power of Infrared
MRT Home Inspections Article - 06/2022 | by Tyler Cole
When asked which tool of the trade is the most valuable for a home inspector, I immediately pull out my E5 Flir Infrared camera. This wonderful device is critical in detecting plumbing leaks, roof leaks, radiant heating, as well as hot water and HVAC system temperatures. The following slide show is a collection of some of the most common uses that infrared provides during the inspection process:

Infrared is very useful in evaluating whether each individual radiant heat zone is functioning. As you can see in this photo, the radiant heat loops are clearly visible after just one hour after start up.

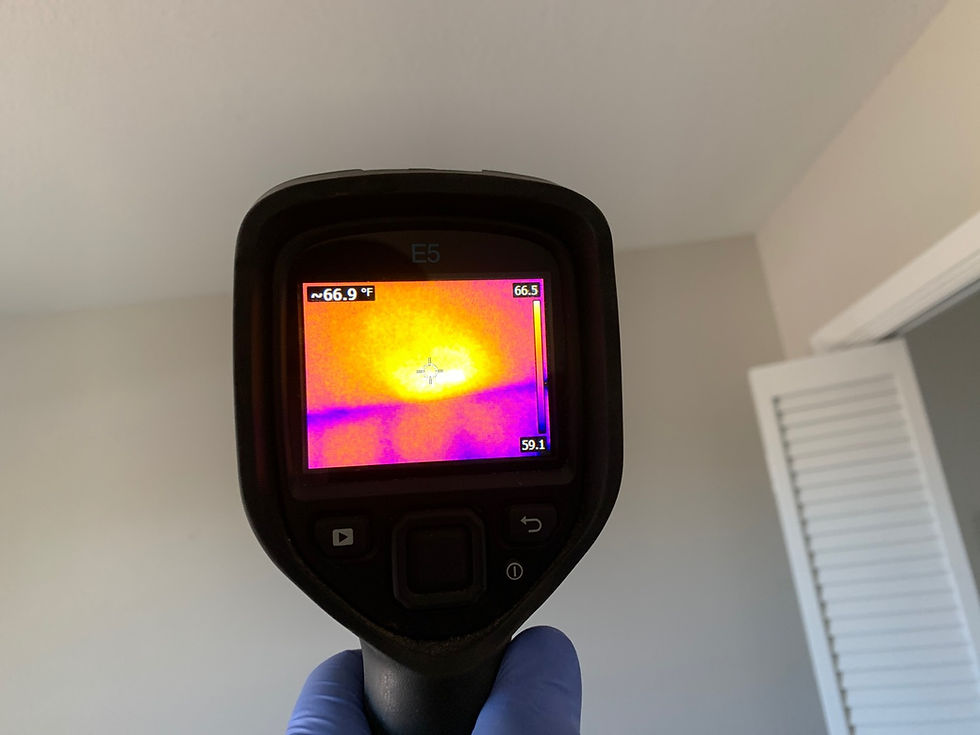
The heat image in this photo turned out to be a colony of bees that had developed in the ceiling plenum of a flat roof home.

Infrared is very useful in evaluating whether each individual radiant heat zone is functioning. As you can see in this photo, the radiant heat loops are clearly visible after just one hour after start up.
The Problem with Drones
MRT Home Inspections Article - 08/2023 | by Tyler Cole
In recent years home inspectors have been promoting the use of drones as cutting edge technology for inspecting roofs. However, the purpose of this short article is to demonstrate why walking the roof is by far a superior method. The basic reason is because there is a loss of depth perception in photos and video that could cause an inspector to miss something important. To illustrate the point, I inspected a two story concrete tile roof home and was ascending to the second level and spotted a large depression in the roof (an observation that would have never been found with a drone). In this case the upper roof had structurally damaged roof trusses that could not be viewed from the attic because there was no attic access. Since, I was physically walking the roof, this major deficiency was observed: slide through the photos below to see if you can spot the issue:

Can you locate the depression?

Can you locate the depression?

Arrow Indicates Depression

Can you locate the depression?
As illustrated in the above photos, it is difficult to see the depression without the arrows directing you to the location. That being said drones or camera poles do have their uses. There are times I have to use a camera pole due to excessively steep roof slopes and for new builds where the builder will not allow the inspector to walk the roof. In conclusion, be wary of home inspectors that boast about the use of drones, because there is a greater chance that something important will be missed.
Common Inspection Issues
MRT Home Inspections Article - 01/2020 | by Tyler Cole
It is common at the onset of an inspection for the client to ask me "So, what are your going to be looking for?" It is a question that is difficult to answer in brief due to the vast variety and scope of issues that may be encountered in a typical inspection. The purpose of this slide show is to give you an idea of the most common issues that may be discovered:

Common Issues: recalled electrical panels (ie Zinsco, Federal Pacific), insufficient panel rating, improper bonding, obstruction and mounting issues.

Common Issues: presence of polybutylene or kitec water piping, corroded and leaking galvanized water piping, active water leaks, excessive water pressure and low water flow issues

Common Issues: cracked casing, seized motor, corroded or leaking drain connections and damaged hammer blades

Common Issues: recalled electrical panels (ie Zinsco, Federal Pacific), insufficient panel rating, improper bonding, obstruction and mounting issues.
Popular Links
